Today, approximately 95% of the world’s hydrogen is derived from fossil fuels, serving primarily as a chemical feedstock across various industries. However, with the increasing focus on zero-emission fuels and the adoption of fuel cell systems, hydrogen’s role in the energy market is expanding rapidly.
Combining these processes with carbon capture, utilization, and storage will reduce the carbon dioxide emissions. Natural gas reforming is an advanced and mature hydrogen production process that builds upon the existing natural gas infrastructure. Today 95% of the hydrogen produced in the United States is made by natural gas reforming in large central plants. This is an important pathway for near-term hydrogen production.
In India, this transition towards clean energy is gaining momentum, fueled by initiatives like the National Green Hydrogen Mission.
In the context of India’s transition towards a sustainable energy future, the sugar and ethanol industry play a significant role in the production of clean hydrogen. With India being one of the world’s largest producers of sugarcane, the sugar industry holds immense potential for clean hydrogen production through biomass to hydrogen production.
While conventional technologies, such as natural gas reforming, currently dominate hydrogen production, concerns about climate change are driving the exploration of alternative, more sustainable methods. Renewable-based processes like solar- or wind-driven electrolysis hold promise for clean hydrogen production, yet further advancements are needed to ensure economic viability. In the Indian context, leveraging the nation’s abundant biomass resources presents a practical and potentially carbon-neutral solution for green hydrogen production.
The International Energy Agency report, “Hydrogen from Carbon-Containing Materials,” highlights the worldwide initiative to explore ways to produce hydrogen with fewer environmental impacts in the near and mid-term. This effort includes large-scale fossil-based production with carbon sequestration, generating hydrogen from biomass, and small-scale reforming for distributed generation.
In India, there’s a keen focus on finding effective ways to convert biomass into hydrogen. This effort aims to meet local market needs and ensure there’s enough biomass available for production. While the report doesn’t cover co-production opportunities, they offer additional ways to make hydrogen production more economically viable.
As India charts its path towards a sustainable energy future, the review of hydrogen production from biomass serves as a strategic tool to guide decision-making and accelerate the adoption of clean hydrogen technologies. By leveraging renewable resources and fostering innovation, India is poised to emerge as a global leader in green hydrogen production, contributing to a cleaner, greener planet for future generations.
Hydrogen, as an energy carrier, is becoming crucial for achieving decarbonization of hard-to-abate sectors. Many sectors such as iron ore and steel, fertilizers, refining, methanol, and maritime shipping emit major amounts of CO2 , and carbon-free hydrogen will play a critical role in enabling deep decarbonization. For other high-emitting sectors, such as heavy-duty trucking and aviation, hydrogen is among the main options being explored with an outlook to be the preferred solution for several applications.
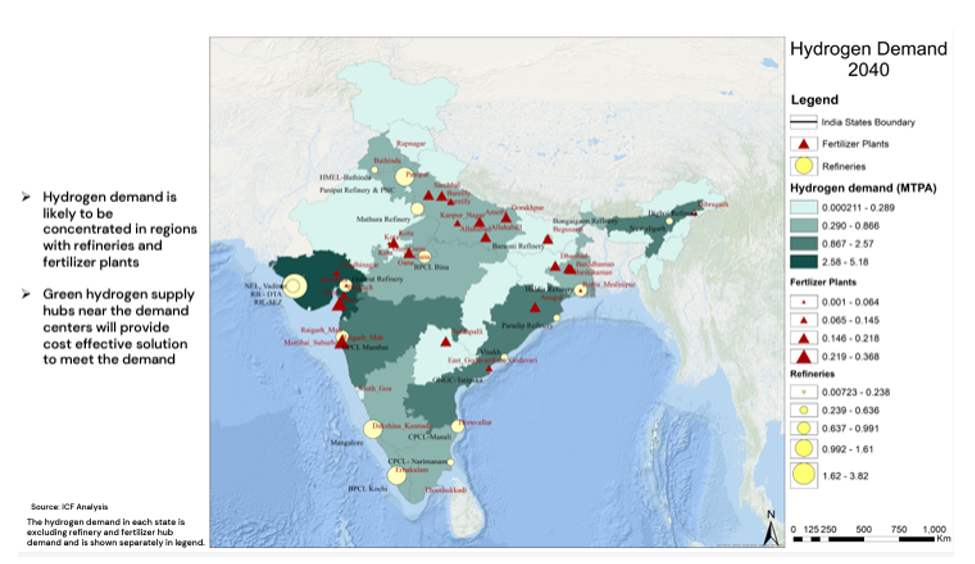
Hydrogen Production Technology:
Producing hydrogen involves various technologies tailored to specific needs and available resources. Here’s an overview of common methods:
Steam Reforming of Natural Gas: This widely used method heats natural gas, primarily methane, with water vapor in the presence of a catalyst. This process breaks down methane, yielding hydrogen and carbon monoxide. While cost-effective, it emits carbon dioxide, impacting the environment.
Electrolysis of Water: Water electrolysis splits water into hydrogen and oxygen using an electric current. Electrolyzers facilitate this process.
Solar Hydrogen Production: This approach utilizes solar energy instead of electricity for electrolysis, either directly or via concentrated solar radiation. It offers cost-effectiveness in regions with ample sunlight.
Thermochemical Hydrogen Production: Certain microorganisms, like bacteria or algae, produce hydrogen through fermentation or photosynthesis. Although promising for sustainability, this method has limited scalability.
Sustainability of hydrogen production hinges on the energy source and CO2 emissions during production. Utilizing renewable energy sources like solar, wind, or hydropower drastically reduces CO2 emissions, making hydrogen production more environmentally friendly. This shift is crucial for achieving a low-carbon future and combatting climate change.
Among hydrogen production technologies, electrolysis stands out as promising, especially when powered by renewable energy sources. Two primary electrolysis methods are PEM and alkaline electrolysis:
PEM Electrolysis: It swiftly splits water into hydrogen and oxygen using a polymer membrane, offering advantages like quick start-up, high efficiency, and compact size. However, it’s sensitive to water impurities and incurs higher costs.Alkaline Electrolysis: This method employs an alkaline electrolyte to split water, boasting lower costs, robustness against contaminants, and longer service life. Yet, it operates at higher temperatures and has slower reaction rates compared to PEM electrolysis.
SOEC (Solid Oxide Electrolysis Cell): Operating at high temperatures, SOEC converts water into hydrogen and oxygen using solid oxides. While efficient, it requires expensive materials and has limited operating experience.
AEM Electrolysis (Anion Exchange Membrane): AEM electrolysis, utilizing a special membrane, offers lower costs and robustness against contaminants. However, it faces challenges in development and commercialization.
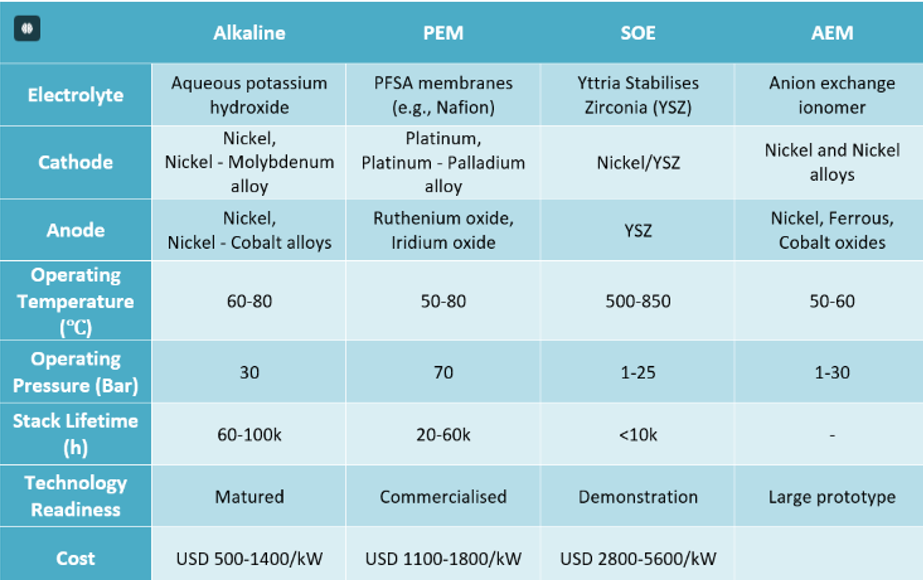
These technologies play a pivotal role in making clean hydrogen a sustainable energy carrier for various applications. Despite their differences, each method contributes to advancing the hydrogen economy, fostering a cleaner, greener future.
Most Economical Technology for Hydrogen Production:
In terms of cost-effectiveness, biomass to hydrogen is often considered the most viable and Steam Methane reforming is economical method for large-scale hydrogen production. SMR benefits from the widespread availability of natural gas as a feedstock and well-established infrastructure. However, it’s crucial to consider the associated carbon emissions and the requirement for carbon capture and storage (CCS) technologies to mitigate environmental impact.
3. Technology Suitable for the Sugar Industry and Why:
Biomass in India
The Indian Institute of Science (IISc) Bangalore has conducted two phases of biomass resource assessment, one during 1998-99 and the other from 2002-04. These assessments aimed to estimate biomass generation, surplus biomass availability, and associated power potential. According to the study, India’s biomass availability was approximately 500 million metric tonnes (MMT), with around 120-150 MMT classified as surplus biomass. This surplus biomass holds the potential to generate an estimated 18,000 MW of power, encompassing agricultural and forest residues. Biomass is an essential RE (Renewable Energy) source because it is widely available, carbon-neutral, capable of providing firm energy and generating significant employment in rural areas. Biomass serves as a prevalent energy source for numerous small-scale industries and independent power plants. Various biomass materials are utilized for power generation, encompassing sugarcane bagasse alongside other non-bagasse materials such as rice husk, straw, cotton stalk, coconut shells, soybean husk, de-oiled cakes, coffee waste, jute waste, groundnut shells, sawdust, and more.
For the sugar industry, which produces significant biomass feedstock such as bagasse, biomass gasification emerges as a promising option for hydrogen production. Biomass gasification involves converting biomass into a hydrogen-rich syngas through thermal decomposition. This technology is well-suited for the sugar industry due to:
• Utilization of Bagasse: Biomass gasification enables the sugar industry to use bagasse, a byproduct of sugarcane processing, as a renewable feedstock for hydrogen production, adding value to the sugar production process.
• Carbon-Neutral Hydrogen Production: Biomass gasification can be configured to produce hydrogen in a carbon-neutral manner, aligning with sustainability goals. The carbon dioxide emitted during gasification is offset by the carbon dioxide absorbed by the biomass during its growth, making it an environmentally friendly option.
• Integration with Existing Infrastructure: Many sugar mills already have biomass boilers or cogeneration plants for generating heat and electricity from bagasse. Biomass gasification can be integrated into these existing facilities, leveraging infrastructure and expertise.
In conclusion, while steam methane reforming (SMR) remains the most economical option for hydrogen production at scale, biomass gasification holds promise for the sugar industry due to its compatibility with biomass feedstocks, carbon-neutral potential, and integration with existing infrastructure. As technology continues to evolve and costs decline, biomass gasification could become an attractive pathway for sustainable hydrogen production in the sugar industry.
Hydrogen Production Method: SMR
1) Why Is Steam Methane Reforming (SMR) Being Considered? Reforming low-cost natural gas is a viable option for producing hydrogen. However, in the long term, natural gas-based hydrogen production will be replaced by production from water electrolysis.
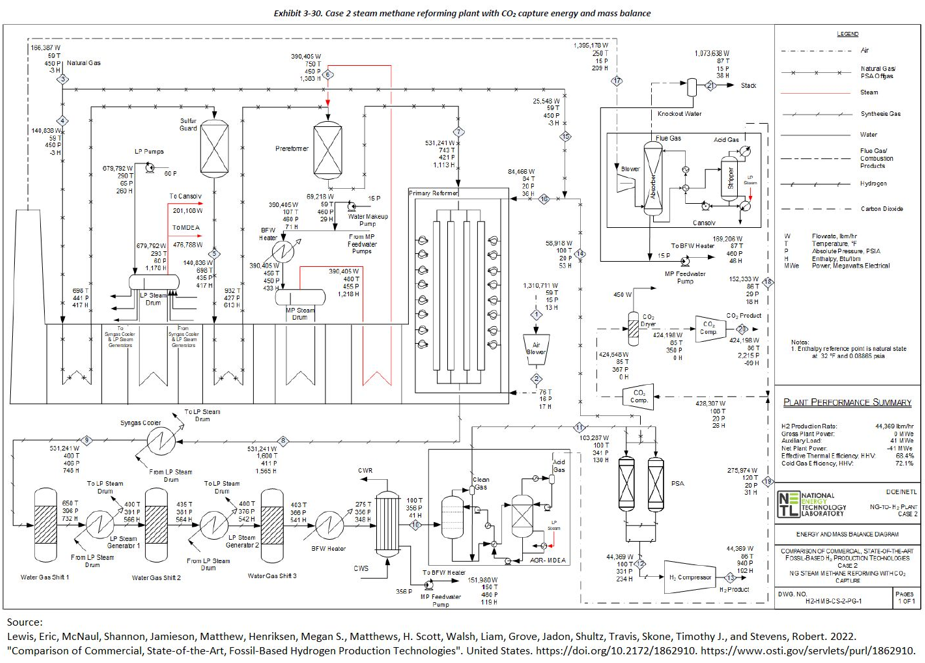
According to the IEA 2023, low-emissions hydrogen accounts for less than 1% of overall hydrogen production and use.
2) How does the Steam Methane Reforming (SMR) plant work?
A gas and steam mixture is reacted over a nickel-based catalyst inside a high alloy steel tube system in the primary steam methane reformer, where partially reformed gas and steam effluent are used.
CH4+H2O↔CO+3H2; Δ𝐻°rxn=205.8 kJ/mol
The process uses a high steam-to-carbon ratio and high temperature to convert over 77% of the methane in the primary reformer feed.
The flue gas path of the fired reformer is integrated with boiler surfaces to produce steam for export or for the regeneration of CO2-removal solvents.
3) Steam Methane Reforming (SMR) Process System:
– Natural Gas Supply System
– Sulfur Polishing
– Prereformer
– Water Gas Shift Reactors
CO+H2O ↔CO2+H2; Δ𝐻°rxn=−41.2 kJ/mol
– Pressure Swing Adsorber (hydrogen production)
4) SMR Plant Major Equipment List
4.1 Primary Reformer
Type: Steam Methane Reformer (SMR), side-fired, fixed bed, catalytic
Design Condition: Syngas Production: 265,000 kg/hr @ 2.8 MPa, 871 °C
4.2 Prereformer
Type: Fixed Bed, catalytic
Design Condition: NG In: 70,000 kg/hr @ 2.9 MPa, 500 °C, Steam In: 195,000 kg/hr @ 3.1 MPa, 399 °C
4.3 Water Gas Shift Reactors
Type: Fixed bed, catalytic
Design Condition: 88,000 kg/hr, 204 °C, 2.8 MPa
4.4 Pressure Swing Adsorber
Type: Polybed Proprietary
Design Condition: Syngas: 171,320 kg/hr, 38 °C, 2.5 MPa
Hydrogen: 20,126 kg/hr, 38 °C, 2.4 MPa, Off Gas: 151,195 kg/hr, 38 °C, 0.1 MPa
4.5 Hydrogen Compressor
Type: Integrally geared, multi-stage centrifugal
Design Condition: 73 m3/min @ 6.5 MPa
Flue Gas Cleanup
4.6 Cansolv
Type: Amine-based CO2 capture technology
Design Condition: 696,000 kg/hr, 12.0 wt % CO2 concentration
4.7 CO2 Dryer
Type: Triethylene glycol
Design Conditions: Inlet: 63 m3/min @ 2.5 MPa
Outlet: 2.4 MPa, Water Recovered: 204 kg/hr
4.8 CO2 Compressor
Type: Integrally geared, multi-stage centrifugal
Design Conditions: 7.0 m3/min @ 15.3 MPa, 85 °C
4.9 CO2 Aftercooler
Type: Shell and tube heat exchanger
Design conditions: Outlet: 15.3 MPa, 30 °C
Duty: 32 GJ/hr
5) Cost Estimation:
5.1- SMR without CO2 capture
SMR plant TOC without CO2 capture is $713/[kg H2/day]. The LCOH is $1.06/kg H2.
5.2- SMR with CO2 capture
SMR plant TOC with CO2 capture is $1,735/[kg H2/day]. The LCOH is $1.64/kg H2 with CO2 T&S.
Exploring the Global and Indian Hydrogen Energy Landscape
Hydrogen energy has emerged as a critical component in the transition to cleaner energy sources. In this post, we explore the global and Indian status of hydrogen supply and demand, examining where hydrogen is used and how it is produced. Let’s dive in.
Applications of Hydrogen
Hydrogen is a versatile gas used across various industries and processes. Here are some of the primary applications:
Oil Refineries: Once known for producing hydrogen, refineries are now major consumers of it. They use hydrogen for hydro-treatment processes like hydro desulfurization, hydrocracking, and hydrogenation of heavier feedstocks to produce refined gasoline and diesel.
Chemical Industry: Hydrogen plays a crucial role in the production of ammonia and methanol, essential for fertilizers and other chemicals.
Semiconductor Industry: It is used for silicon passivation in electronics.
Food Industry: Hydrogenation processes involve converting oils into fats for various food products.
Transportation: Although its current use is limited, hydrogen has great potential for long-haul transportation, such as freight vehicles, shipping, and aviation.
Space Applications: Hydrogen’s high energy content per unit mass makes it an ideal fuel for space exploration.Power Generation: Hydrogen is used in gas turbines and stationary fuel cells for electricity generation. It also serves as a storage medium to balance renewable energy’s variable output.
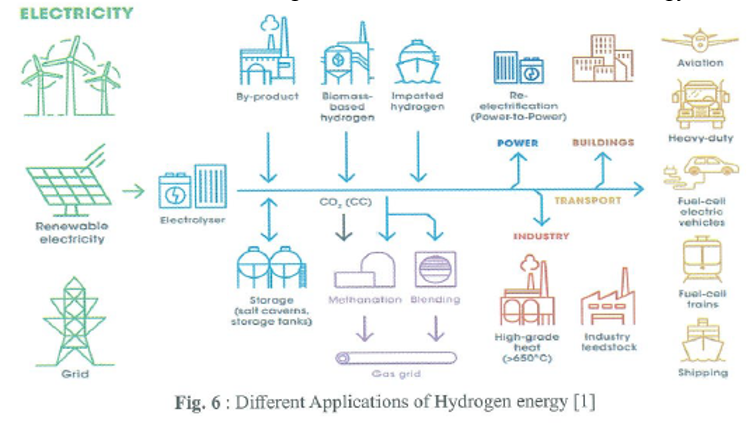
Hydrogen Production Cost:
The cost of hydrogen production varies depending on the method used and factors such as energy source, infrastructure, and scale. Here’s an overview of the cost considerations for different hydrogen production methods:
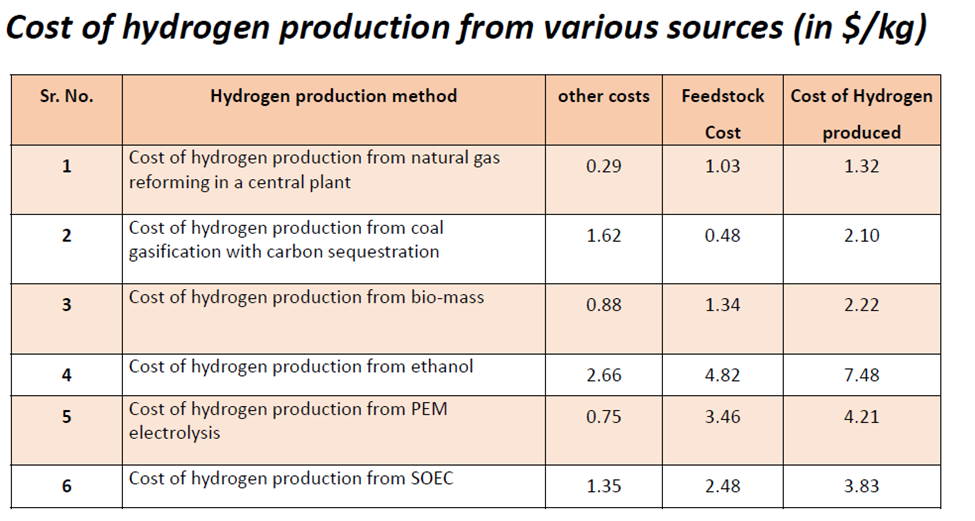
Source NREL
Technology | Advantages | Drawbacks | Energy Efficiency (%) | H2 yield (g/kgfeedstock) | Cost ($/kg of H2 | |
Feed:Water | electrolysis | 55−80 | 111α | 4.15−10.30 | ||
simplicity | high pressure is required | |||||
low temperatures | energy storage problems | |||||
zero carbon emissions | low system efficiencies | |||||
O2 as a byproduct | high capital costs | |||||
integration with fuel cells | ||||||
Thermolysis | clean and sustainable | separation step is required to avoid the recombination in an explosive mixture | 20−50 | 111α | 7.98−8.40 | |
zero carbon emissions | high capital costs | |||||
O2 as a byproduct | ||||||
Photoelectrolysis | contributes to the sustainability of the energy supply | low efficiency | 0.06−14 | 111α | 4.98−10.36 | |
photonic and electrical energies can be converted to chemical energy | requires a significant surface | |||||
low operating temperature and pressure | photocatalytic material is required | |||||
Biophotolysis | can produce hydrogen at ambient conditions | requires a significant surface area to collect enough sunlight | 10−15 | 111α | 1.42-2.13 |
Technology | Advantages | Drawbacks | Energy Efficiency (%) | H2 yield (g/kgfeedstock) | Cost ($/kg of H2 | |
Feed: Biomass | dark fermentation | can produce hydrogen at any time because light is not required | 60−80 | Apr-44 | 1.68−2.57 | |
ambient conditions | hydrogen yield is metabolically restricted | |||||
simple reactor design | high byproduct generation | |||||
waste recycling | low efficiency | |||||
large reactor volume | ||||||
pyrolysis | developed technology | 35−50 | 25-65 | 1.59−2.20 | ||
abundant and cheap feedstock | hydrogen yield depends upon the feedstock | |||||
solid, liquid, and gas product streams | tar formation | |||||
carbon-neutral emissions | requires oxidation agents | |||||
gasification | abundant and cheap feedstocks | hydrogen yield depends upon the feedstock | 30−60 | 40-190 | 1.77-2.05 | |
carbon-neutral emissions | tar formation | |||||
steam reforming | developed technology | 74−85 | 40-130 | 1.83−2.35 | ||
avoid the costly upgrading of the bio-oil | produce carbon co-products | |||||
Understanding profitability in the hydrogen industry
It requires knowing about different factors like market demand, production costs, and pricing changes. Investors and stakeholders use financial indicators such as EBITDA and ROCE to
assess profitability and decide if investing in hydrogen is a good idea. Here are some key points to understand:
Market Demand: Profitability depends on how much hydrogen is needed in industries like transportation and energy storage. Changes in regulations, technology, and consumer preferences affect demand. High demand can mean better prices, but disruptions can lead to challenges.
Production Costs: Making hydrogen products costs money, which affects profits. Costs include things like raw materials, energy, and investments in equipment. Investing in new technology and improving processes can help reduce costs and increase profits.
Pricing: Prices for hydrogen are influenced by supply, demand, competition, and regulations. Companies need to find the right balance between competitiveness and profits when setting prices. Understanding the market and predicting trends is important for success.
Financial Metrics: EBITDA and ROCE are important measures for assessing profitability. EBITDA shows how well a company is doing without certain costs, while ROCE looks at how efficiently it’s using capital to generate returns. Investors use these metrics to evaluate hydrogen projects.
Policies and Regulations: Government rules and support can affect hydrogen profits. Incentives, subsidies, and carbon pricing can shape the market and investment decisions. Policies that encourage renewable hydrogen and infrastructure growth can help businesses succeed.
India’s Approach to creating a Clean Hydrogen Economy
India recognizes the importance of transitioning to a clean Hydrogen economy to advance its clean energy goals and reduce dependence on crude oil and natural gas imports. The government has launched the National Green Hydrogen Mission to position India as a global hub for producing and exporting Green Hydrogen by increasing domestic production capacity. This mission aims to add renewable energy capacity, attract significant investment, create jobs, and mitigate greenhouse gas emissions.
To support Clean Hydrogen production, infrastructure development is crucial. Projects are being set up in coastal areas due to ease of exports. Establishing Green Hydrogen Manufacturing Hubs and enabling the transfer of renewable power to these hubs can accelerate production. Additionally, creating desalination plants for water supply and pipeline infrastructure for transportation are essential components.
Encouraging consumption of Clean Hydrogen is vital for market growth. Similar to renewable energy mandates, government mandates may be introduced to promote Clean Hydrogen consumption in sectors like refining, fertilizers, and steel. Mandating blending of Green Methanol, derived from Hydrogen, can also boost energy security efforts.
Conclusion: International cooperation is essential for exporting Clean Hydrogen and its derivatives. India can leverage its diplomatic relations to create a level playing field and capture a share of the global market. Collaboration with countries facing resource constraints can facilitate trade agreements under provisions like Article 6 of the COP agreement. Clean Hydrogen offers a promising solution for India’s energy security and sustainability. By focusing on infrastructure development, consumption mandates, and international cooperation, India can strengthen its energy security, reduce carbon emissions, and transition towards a sustainable future. In conclusion, securing profitable returns for hydrogen products necessitates a thorough understanding of market dynamics, production expenses, pricing strategies, and regulatory policies. Firms must employ a strategic approach to maximize profitability while balancing operational efficiency, risk management, and stakeholder expectations. By harnessing advanced technologies, fostering innovation, and staying in sync with evolving market trends, stakeholders in the hydrogen sector can tap into opportunities for sustainable growth and contribute to a cleaner, more resilient energy future.
Sources:
Ministry of New and Renewable Energy (MNRE), Government of India, Press Information Bureau, Government of India, International Renewable Energy Agency (IRENA), Fuel Cell and Hydrogen Energy Association (FCHEA)
Disclaimer: The views and opinions expressed in the article by Dilip Patil, Managing Director of Samarth SSK Ltd., are solely his own.
To read more about Green Hydrogen Industry News, continue reading BioEnergyTimes.com